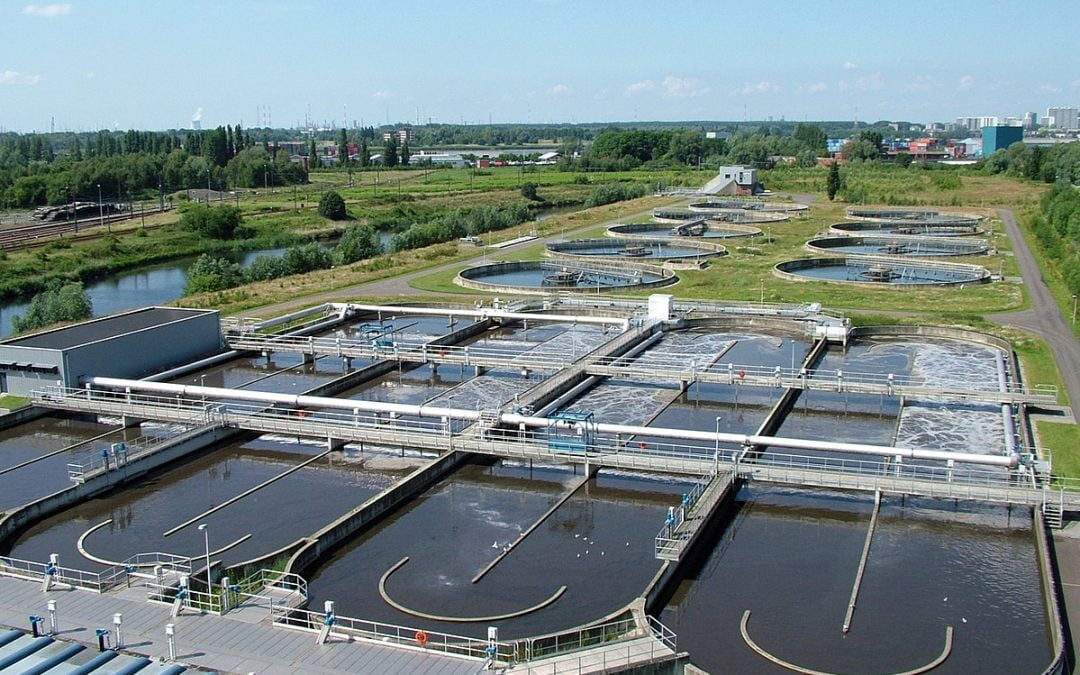
Activated sludge system
The activated sludge process is a type of waste water treatment process for treating sewage or industrial waste waters using aeration and a biological floc composed of bacteria
The process takes advantage of aerobic micro-organisms that can digest organic matter in sewage, and clump together (by flocculation) as they do so. It thereby produces a liquid that is relatively free from suspended solids and organic material, and flocculated particles that will readily settle out and can be removed. AOPL undertakes erection and commissioning of Activated Sludge systems in association with authentic technology suppliers in India & Outside
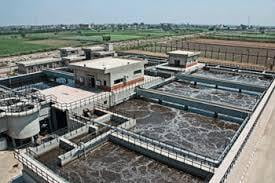
Sequential Batch Reactor Systems
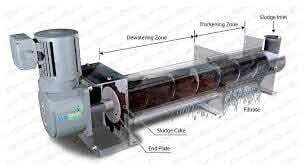
Sludge Pressing Units
Biological effluent treatment systems are followed by sludge press units which helps to reduce the moisture content in the ETP biosludge and make them ready for disposal
Anaerobic Reactors
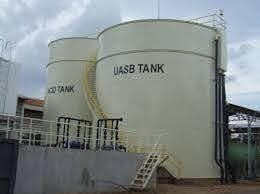
UASB Reactors
Invented during the 1970’s, an UASB reactor essentially works by forming a blanket of sludge which remain suspended in the tank. The waste water would flow upwards through the sludge thus getting the bacteria present in the sludge in contact with the COD which is converted to Biogas. This process relies on gravity to keep the biomass in place as biomass is the key component in the removal of COD from water. The sludge blanket is able to deal with both solid and liquid pollutants but has to be constantly monitored to prevent sludge wash out. COD present in the water can be converted to Bio gas in around a days time. It does conversion rate around 80%
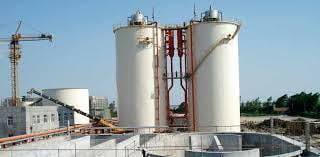
Internal Circulation Reactors
The IC reactor was invented after the UASB reactor as a method to address the drawbacks of the UASB reactor. Quite frankly an IC digester is a third generation evolution of a UASB digester. This digester typically produces biogas with a very high concentration of methane compared to UASB. The forced circulation design combined with a two stage sludge separation process ensures that there is a very high contact with the biomass and the wastewater resulting in higher biomass activity. This ensures a very high conversion of COD to Biogas. Additionally the two stage sludge separation system ensures that there is no biomass slipping out of the system. The high biomass concentration makes the biomass to agglomerate into granules which are easier to separate from water and allows it to reduce the time taken to reduce COD to a fraction of the time taken in a UASB reactor.
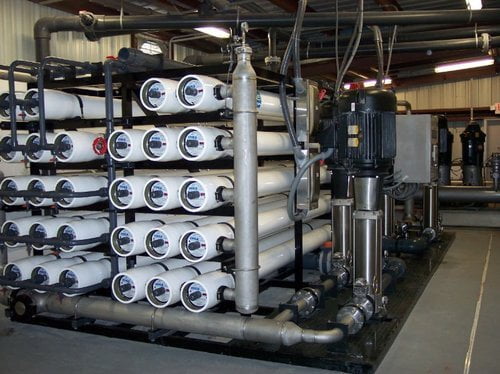
DM Plant & RO Plants
Demineralised Water is Water completely free ( or almost ) of dissolved minerals as a result of one of the following processes :
●Distillation
●Deionization
●Membrane filtration (reverse osmosis or nanofiltration)
●Electrodyalisis
●Or other technologies.
Demineralized Water also known as Deionized Water, Water that has had its mineral ions removed. Mineral ions such as cations of sodium, calcium, iron, copper, etc and anions such as chloride, sulphate, nitrate, etc are common ions present in Water. Deionization is a physical process which uses specially-manufactured ion exchange resins which provides ion exchange site for the replacement of the mineral salts in Water with Water forming H+ and OH- ions. Because the majority of Water impurities are dissolved salts, deionization produces a high purity Water that is generally similar to distilled Water, and this process is quick and without scale buildup. De-mineralization technology is the proven process for treatment of Water. A DM Water System produces mineral free Water by operating on the principles of ion exchange, Degasification, and polishing. Demineralized Water System finds wide application in the field of steam, power, process, and cooling. AOPL under take erection & commissioning of DM & RO plants for various industries
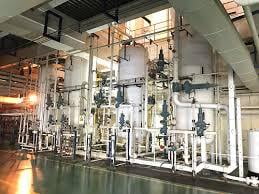